If you are to ask drystock or tillage farmers, who have ample land around the yard, why they wouldn’t convert to dairy farming despite the obvious higher margins, one of the most likely responses would be “I don’t want to be tied to the farm, milking morning and evening”.
To dairy farmers’ credit, in recent years they have adopted 16:8 milkings to finish earlier, with ‘10 in seven’ now being trialled by some to reduce the amount of milkings completed.
Conventional parlours still require a person to be there for milking, and with farm labour becoming increasingly difficult to find, many farmers are turning to automation of the milking routine as an alternative.
Noel Lynch is a well-known figure around the Callan area in Kilkenny, operating Lynch Fencing, with him and his team completing agri, domestic and industrial fencing in the locality. Alongside the fencing business, Noel runs a 34ha farm, which previously had a herd of suckler cows.
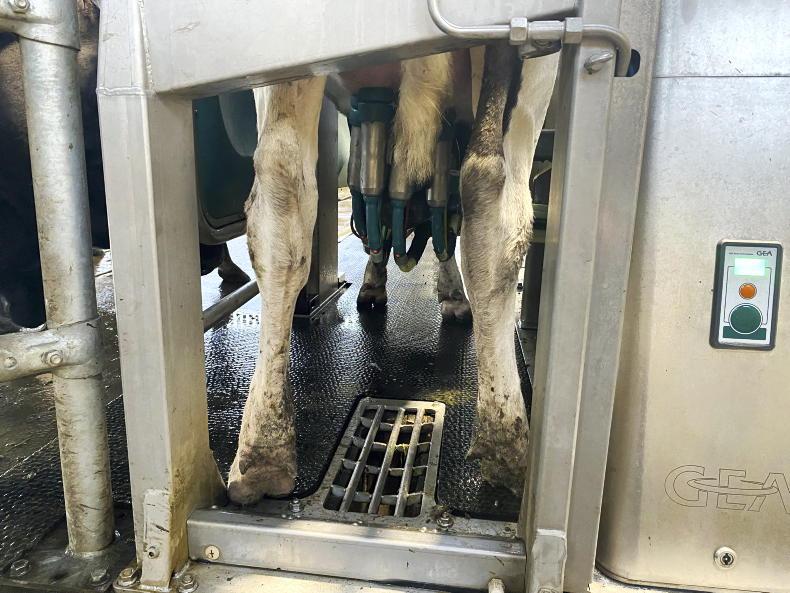
The view of the cow's udder from the pit. The cluster performs washing, stripping out, milking and post-dipping of the teat.
Converting
Prior to getting into sucklers, there was 40 dairy cows milked up to 2002. Noel returned home from Harper Adams, and wishing to use his degree he began travelling and working within the agricultural industry, some of which involved milking cows in various parlour setups. The old parlour on the Lynch farm had been a herringbone six-unit, which Noel had ripped out and the dairy converted to a suckler calving area.
While it was initially planned to put the robot and dairy in the old dairy unit, Noel decided against this after seeing the potential in a three-bay beef slatted shed, and through changing the internal lay out and adding a two-bay extension, the conversion now sits smoothly in the former beef shed.
“We started digging on 8 August last year, and we were milking on 25 January’’ explained Noel, with Noel and his fencing team completing all the fabrication and concrete works, excluding the installation of the robot.
The central feed passage of the three-bay shed was suspended, with Noel and his crew ripping out the solid slabs and concrete overlay and replacing them with specially made 8ft 10in slotted cattle slats.

The pit area offers ease of access for servicing the machine or treatment of cows.
Why a robot and why GEA?
With the fencing business so busy, Noel was looking to add value to the farm and prevent it being a loss-making enterprise without dramatically increasing the workload.
By his own admission, Noel says: “My life got a lot easier managing dairy cows rather than 70 to 80 suckler cows, which I had here. If I’m not back until 10 o’clock at night, cows are still milked with the robot.
“My workload with the cows is reduced to a small amount of cleaning of the machine, changing the milk sock and setting up fences. Labour is extremely difficult to source around here.’’
As to why he chose GEA, Noel explained that having a local sales and service team and the pit installed around the robot were the two main benefits.
“I think the technology is a little better than some of the other competitors. I had a cow that cut her teat the other day, but I could stand in the pit and put the cluster on her.”
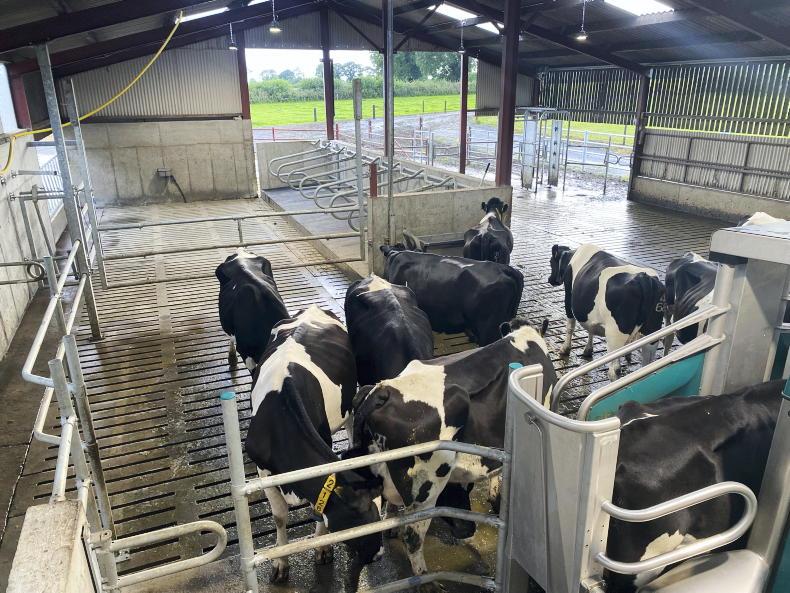
The layout of the shed, with cows drafted to the back of the robot and through the chute seen on the left to the small cubicle area for breeding, treatment, etc.
Ease of management
Cleaning, servicing and treating cows are all made simpler by having a pit, in Noel’s view. When treatment is needed, eg for mastitis, Noel will get the robot to draft the cow to the holding area post milking, where she will wait until Noel gets back to the yard and allows her access to the robot again.
With the cow in the robot, Noel can go down in to the pit and have easy access to the udder. There is a light fitted underneath to make it easy to see, while a dung box helps keep the area clean.
A sprinkler system keeps the rubber matting that the cows stand on wetted to make it easier to hose off. The milking arm itself is impressive, acting in a similar way to the traditional cluster; moving with the cow if she moves around. The gyro arm attaches the cluster to the teat via a small 3D camera.
The cluster itself cleans the teat, strips it out, milks and applies post-milking teat dip. Information from each individual teat such as milk temperature, cell count and kilos of milk are all retained, with irregularities flagged on the software.
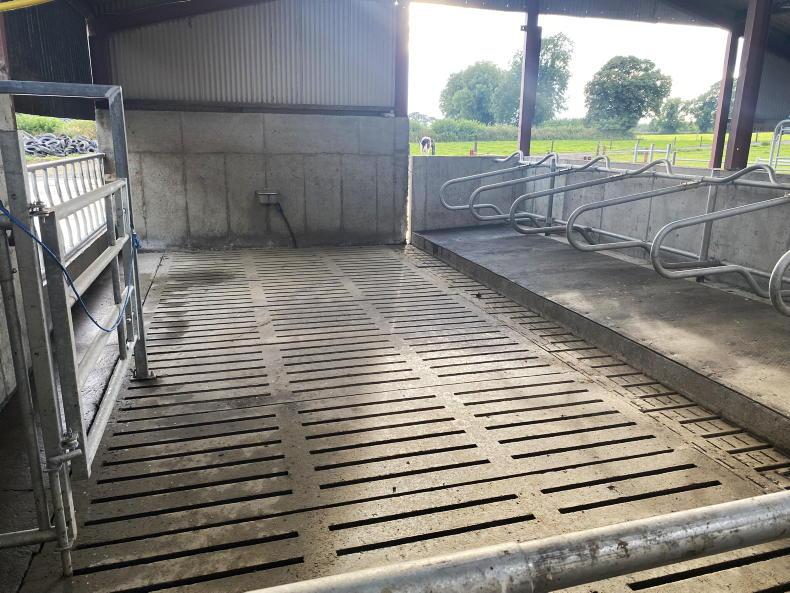
Eight cubicles, a drinker, feed barrier and a handling crush were installed in the drafting area.
Robot shed layout and grazing
The entire old three-bay shed is slatted and acts as the lounge area pre- and post-milking, with the two new bays, which were planning exempt due to the size, house the dairy, storage area, plant room and upstairs office.
Noel created two robotic pits side by side, with the plan being to install a second robot in 2025 as the herd increases in size and matures.
On the left side of the shed, Noel has created an eight-cubicle drafting area with non-return gates, with a feed barrier, trough and handling area, fitted with an up and over gate.
Beside this is a bungee gate that Noel extended. When training heifers in spring, Noel and his team use this to help divert fresh calved heifers in to the robot.
At the rear right hand corner are two non-return (Texan) gates allowing entry to the shed, while a GEA drafting gate diverts the cows to either block A or B.
Noel is currently tweaking the grazing regime, with a fresh paddock opened every six hours. “Some cows were leaving block A when it was grazed out, going to be milked and then arriving at block B to it being nearly grazed, which was hitting their production.’’
Due to the current narrow profile of the farm, a C block is not yet viable, so Noel is seeing will the above regime work.
The farm had an existing road network running through it due to its dairy history, so Noel created a 2m wide roadway along each of the main roadways to service the robot and allow cows pass each other exiting and entering paddocks. The main roadway is then used for machinery access as well.
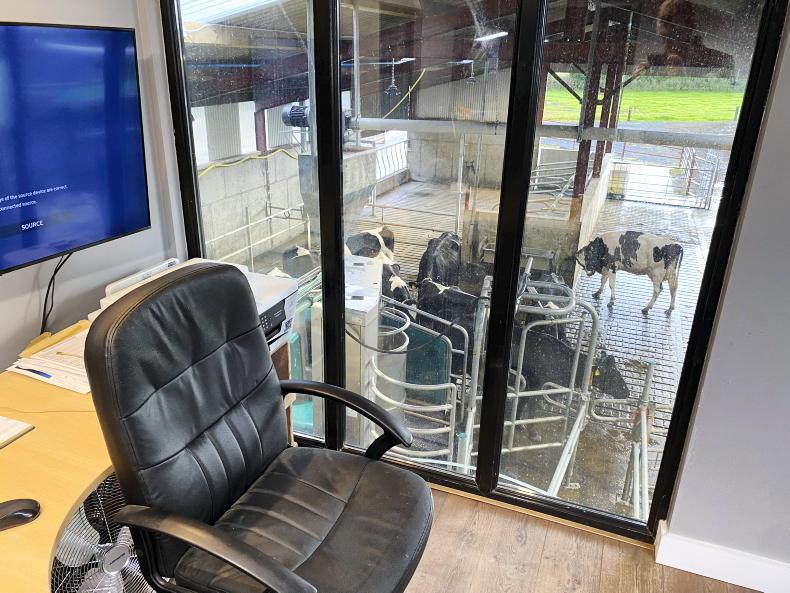
The view of the robot area from the office window.
Milk storage
and power
In an effort to keep to a budget, Noel installed a secondhand 8,000-litre bulk tank, with the GEA robot coming with the necessary retrofits to adapt it to an automatic milking system.
Noel feels that even this size of a tank is sufficient should he push cow numbers to 100. A roller door was installed in front of the tank, should he wish to replace it in a few years.
Any waste milk for calves comes in to the dairy on a separate line and is pumped in to the milk trolley, with an option to pump this directly to calf housing. Behind the dairy will be a toilet and shower area, while adjoined to this is the storage area for chemicals as well as a plant room. Upstairs is the office area, which looks down over the lounging area and robot.
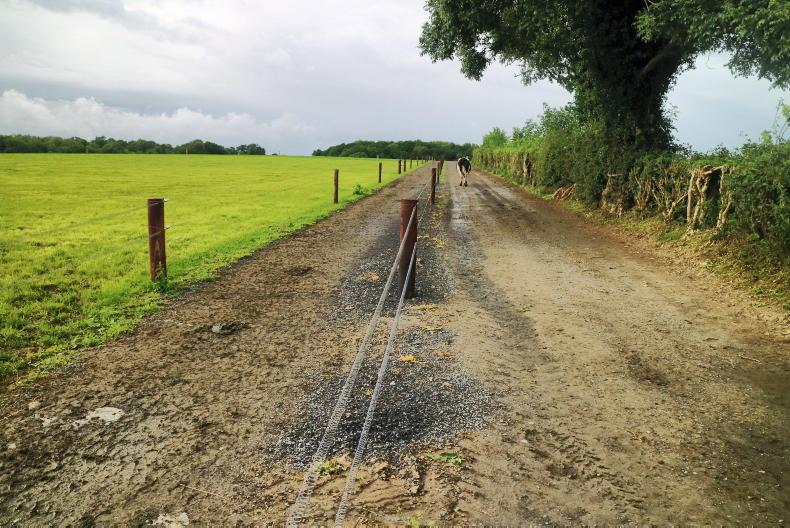
Cost
Noel and his team completed a huge amount of work themselves which should be noted in the financial costs. The project to convert the farm included the two wide roads, an additional 40 cubicles, the conversion works and extension of the beef slatted shed, as well as the robot and bulk tank. All in all, the conversion (excluding stock) €250,000 was spent (including VAT). With the VAT back and €29,000 of TAMS aid for the robot received, Noel will be looking at a cost of conversion of roughly €170,000. While there are 82 cubicles on the farm, additional slurry storage and a re-roofing of some of the cubicle area will mean additional spending down the line.
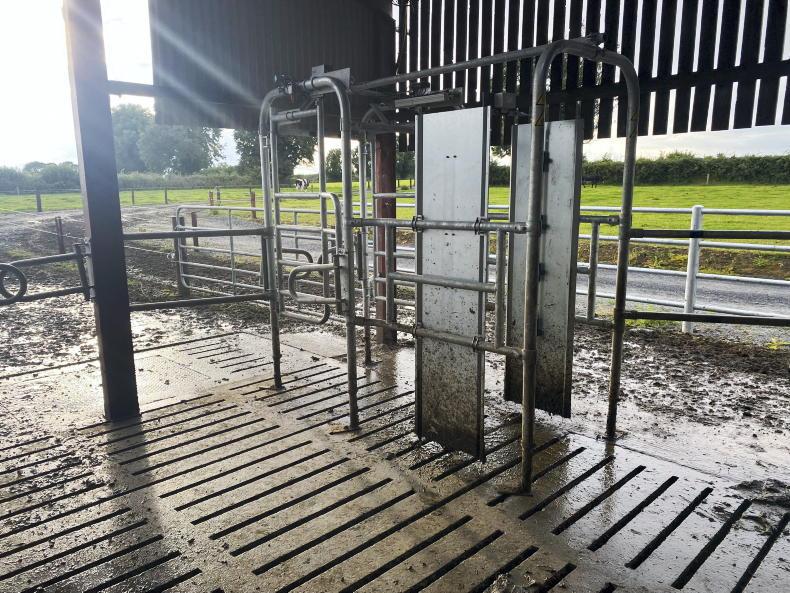
The drafting gate sends the cows to either the A or B block.
If you are to ask drystock or tillage farmers, who have ample land around the yard, why they wouldn’t convert to dairy farming despite the obvious higher margins, one of the most likely responses would be “I don’t want to be tied to the farm, milking morning and evening”.
To dairy farmers’ credit, in recent years they have adopted 16:8 milkings to finish earlier, with ‘10 in seven’ now being trialled by some to reduce the amount of milkings completed.
Conventional parlours still require a person to be there for milking, and with farm labour becoming increasingly difficult to find, many farmers are turning to automation of the milking routine as an alternative.
Noel Lynch is a well-known figure around the Callan area in Kilkenny, operating Lynch Fencing, with him and his team completing agri, domestic and industrial fencing in the locality. Alongside the fencing business, Noel runs a 34ha farm, which previously had a herd of suckler cows.
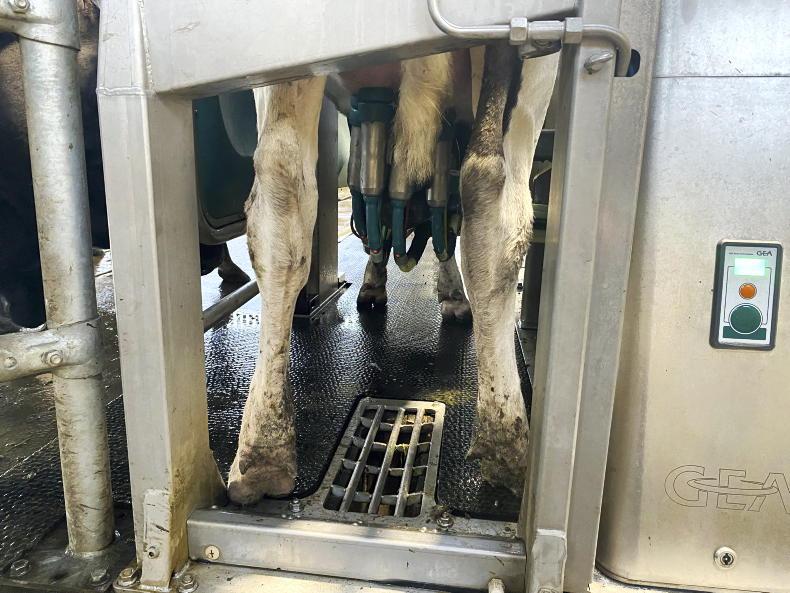
The view of the cow's udder from the pit. The cluster performs washing, stripping out, milking and post-dipping of the teat.
Converting
Prior to getting into sucklers, there was 40 dairy cows milked up to 2002. Noel returned home from Harper Adams, and wishing to use his degree he began travelling and working within the agricultural industry, some of which involved milking cows in various parlour setups. The old parlour on the Lynch farm had been a herringbone six-unit, which Noel had ripped out and the dairy converted to a suckler calving area.
While it was initially planned to put the robot and dairy in the old dairy unit, Noel decided against this after seeing the potential in a three-bay beef slatted shed, and through changing the internal lay out and adding a two-bay extension, the conversion now sits smoothly in the former beef shed.
“We started digging on 8 August last year, and we were milking on 25 January’’ explained Noel, with Noel and his fencing team completing all the fabrication and concrete works, excluding the installation of the robot.
The central feed passage of the three-bay shed was suspended, with Noel and his crew ripping out the solid slabs and concrete overlay and replacing them with specially made 8ft 10in slotted cattle slats.

The pit area offers ease of access for servicing the machine or treatment of cows.
Why a robot and why GEA?
With the fencing business so busy, Noel was looking to add value to the farm and prevent it being a loss-making enterprise without dramatically increasing the workload.
By his own admission, Noel says: “My life got a lot easier managing dairy cows rather than 70 to 80 suckler cows, which I had here. If I’m not back until 10 o’clock at night, cows are still milked with the robot.
“My workload with the cows is reduced to a small amount of cleaning of the machine, changing the milk sock and setting up fences. Labour is extremely difficult to source around here.’’
As to why he chose GEA, Noel explained that having a local sales and service team and the pit installed around the robot were the two main benefits.
“I think the technology is a little better than some of the other competitors. I had a cow that cut her teat the other day, but I could stand in the pit and put the cluster on her.”
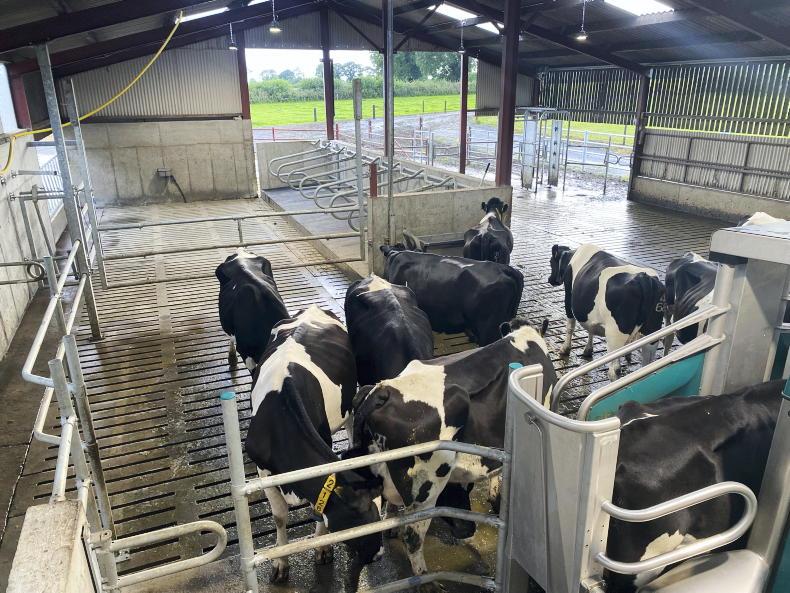
The layout of the shed, with cows drafted to the back of the robot and through the chute seen on the left to the small cubicle area for breeding, treatment, etc.
Ease of management
Cleaning, servicing and treating cows are all made simpler by having a pit, in Noel’s view. When treatment is needed, eg for mastitis, Noel will get the robot to draft the cow to the holding area post milking, where she will wait until Noel gets back to the yard and allows her access to the robot again.
With the cow in the robot, Noel can go down in to the pit and have easy access to the udder. There is a light fitted underneath to make it easy to see, while a dung box helps keep the area clean.
A sprinkler system keeps the rubber matting that the cows stand on wetted to make it easier to hose off. The milking arm itself is impressive, acting in a similar way to the traditional cluster; moving with the cow if she moves around. The gyro arm attaches the cluster to the teat via a small 3D camera.
The cluster itself cleans the teat, strips it out, milks and applies post-milking teat dip. Information from each individual teat such as milk temperature, cell count and kilos of milk are all retained, with irregularities flagged on the software.
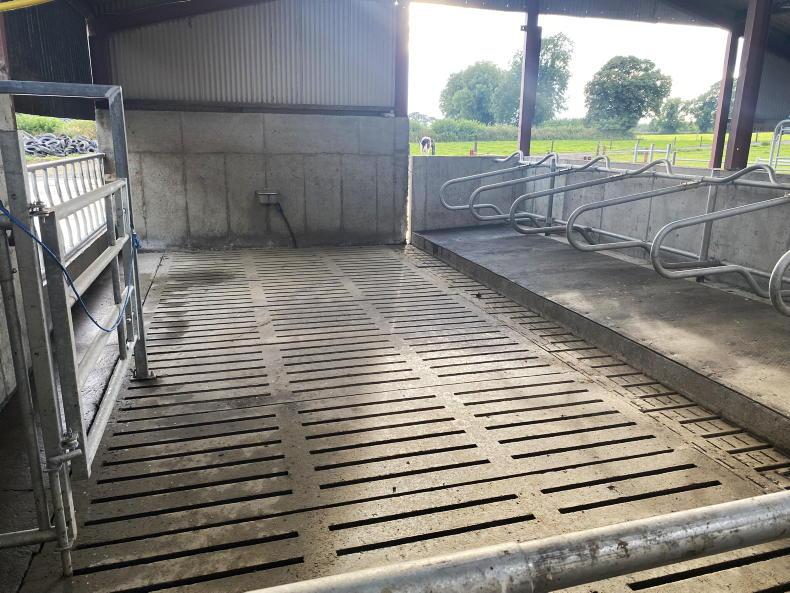
Eight cubicles, a drinker, feed barrier and a handling crush were installed in the drafting area.
Robot shed layout and grazing
The entire old three-bay shed is slatted and acts as the lounge area pre- and post-milking, with the two new bays, which were planning exempt due to the size, house the dairy, storage area, plant room and upstairs office.
Noel created two robotic pits side by side, with the plan being to install a second robot in 2025 as the herd increases in size and matures.
On the left side of the shed, Noel has created an eight-cubicle drafting area with non-return gates, with a feed barrier, trough and handling area, fitted with an up and over gate.
Beside this is a bungee gate that Noel extended. When training heifers in spring, Noel and his team use this to help divert fresh calved heifers in to the robot.
At the rear right hand corner are two non-return (Texan) gates allowing entry to the shed, while a GEA drafting gate diverts the cows to either block A or B.
Noel is currently tweaking the grazing regime, with a fresh paddock opened every six hours. “Some cows were leaving block A when it was grazed out, going to be milked and then arriving at block B to it being nearly grazed, which was hitting their production.’’
Due to the current narrow profile of the farm, a C block is not yet viable, so Noel is seeing will the above regime work.
The farm had an existing road network running through it due to its dairy history, so Noel created a 2m wide roadway along each of the main roadways to service the robot and allow cows pass each other exiting and entering paddocks. The main roadway is then used for machinery access as well.
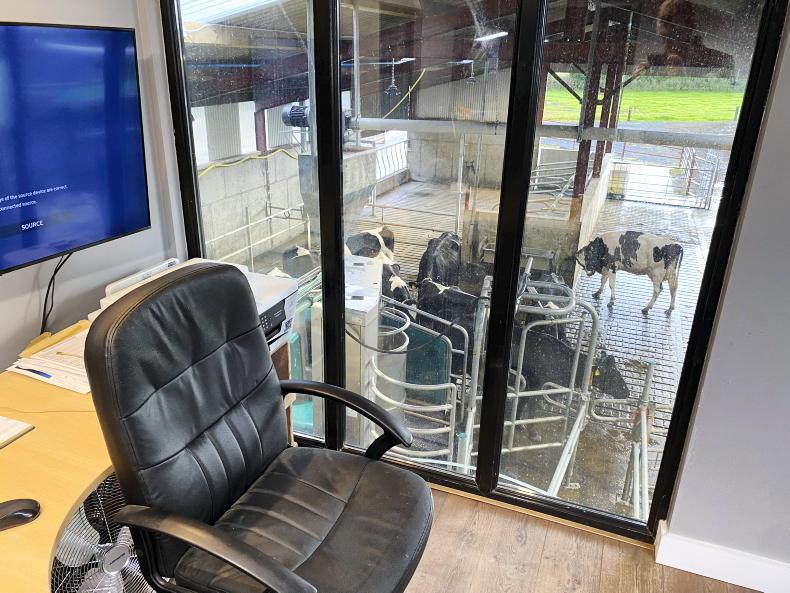
The view of the robot area from the office window.
Milk storage
and power
In an effort to keep to a budget, Noel installed a secondhand 8,000-litre bulk tank, with the GEA robot coming with the necessary retrofits to adapt it to an automatic milking system.
Noel feels that even this size of a tank is sufficient should he push cow numbers to 100. A roller door was installed in front of the tank, should he wish to replace it in a few years.
Any waste milk for calves comes in to the dairy on a separate line and is pumped in to the milk trolley, with an option to pump this directly to calf housing. Behind the dairy will be a toilet and shower area, while adjoined to this is the storage area for chemicals as well as a plant room. Upstairs is the office area, which looks down over the lounging area and robot.
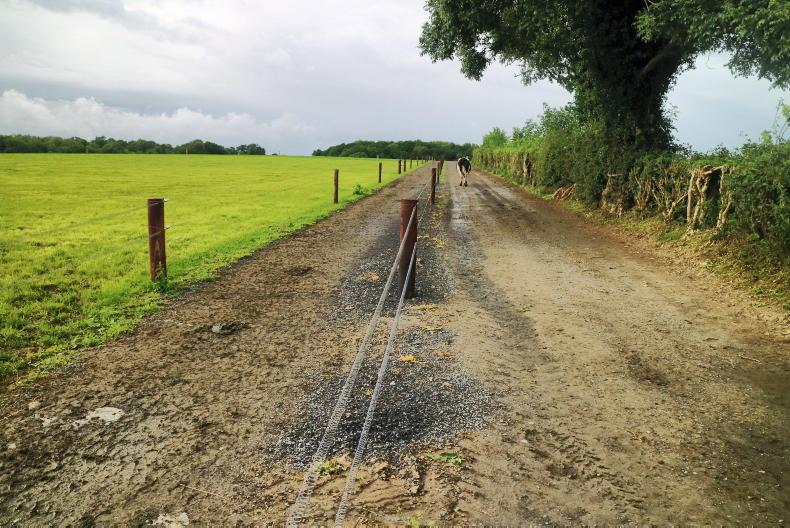
Cost
Noel and his team completed a huge amount of work themselves which should be noted in the financial costs. The project to convert the farm included the two wide roads, an additional 40 cubicles, the conversion works and extension of the beef slatted shed, as well as the robot and bulk tank. All in all, the conversion (excluding stock) €250,000 was spent (including VAT). With the VAT back and €29,000 of TAMS aid for the robot received, Noel will be looking at a cost of conversion of roughly €170,000. While there are 82 cubicles on the farm, additional slurry storage and a re-roofing of some of the cubicle area will mean additional spending down the line.
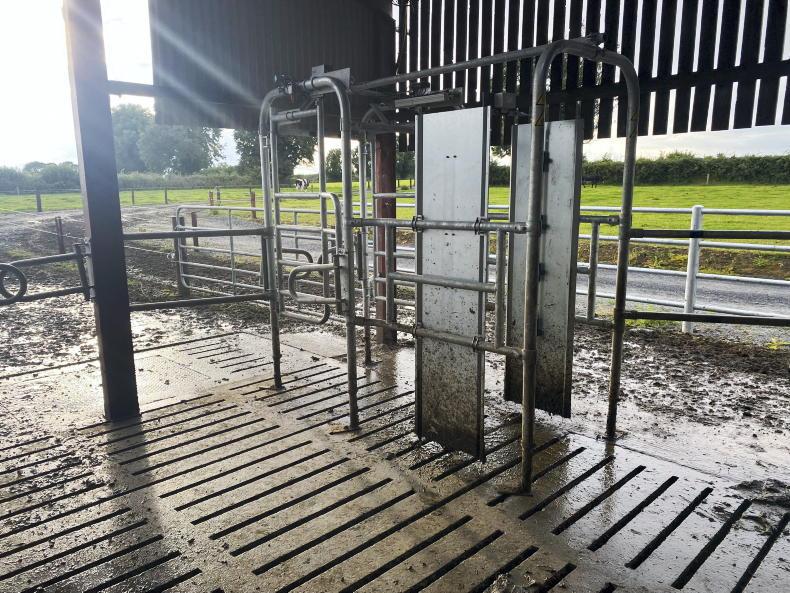
The drafting gate sends the cows to either the A or B block.
SHARING OPTIONS